آشنایی با جوشکاری فلز قوسی دستی (MMA ،SMAW یا جوشکاری چسبی)
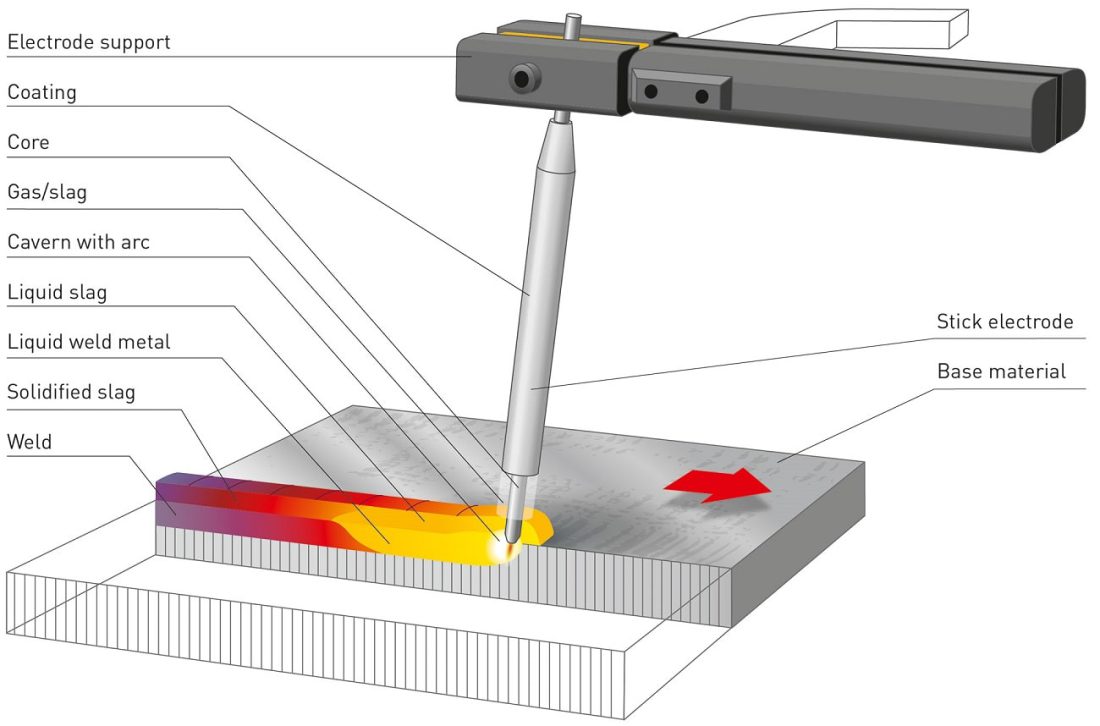
در فرایند جوشکاری فلز قوسی دستی تحت عناوین جوشکاری فلز قوسی با الکترود روکش دار، جوشکاری قوسی پودری محافظ یا جوشکاری چسبی، ما بین الکترود پودری پوشش داده شده بر میله فلزی و قطعه مورد نظر قوس الکتریکی برقرار میشود؛ در این حالت میله و سطح برای ایجاد جوش، ذوب میشوند.
ابتدا در کشور روسیه در سال 1888 جوشکاری فلز قوسی دستی اختراع شد؛ که دارای میله فلزی لخت بدون پوشش پودری جهت ایجاد گاز محافظ بود.
تا اوایل دهه 1900 توسعه و پیشرفتی در الکترودهای پوشش دهی شده به وجود نیامد؛ تا اینکه در سوئد فرآیند کیلبرگ اختراع و روش شبه قوسی در بریتانیا معرفی شد. البته بکارگیری الکترودهای پوشش دهی شده به خاطر هزینه زیاد روند آرامی داشت؛ اما به دلیل افزایش تقاضا در جوشکاری های صوتی، فلز قوسی دستی با الکترودهای پوشش دهی شده اجتناب پذیر بود. ایجاد قوس الکتریکی مابین میله فلزی (الکترود) و قطعه منجر به ذوب الکترود و سطح قطعه شده و در نهایت حوضچه فلز مذاب جوش تشکیل میگردد. تشکیل گاز و سرباره در اثر ذوب همزمان پودر پوشش دهی شده بر روی الکترود، باعث حفاظت حوضچه جوش از محیط اطراف میشود؛ که سرباره منجمد و سرد شده و بعد از تکمیل عملیات جوش (یا قبل از نشست پاس بعدی جوش) باید از مهره جوش جداسازی شود.
در این فرآیند جوشهای زده شده قبل از بکارگیری الکترود جدید در نگهدارنده، طول های کمتری دارند. نفوذ جوش کم بوده و کیفیت نشست جوش نهایی به شدت وابسته به مهارت جوشکار است.
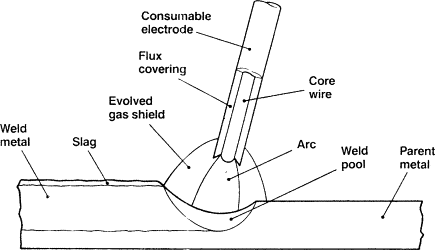
انواع فلاکس (پودر)/ الکترود
برای برقراری قوس الکتریکی مابین الکترود و فلز پایه همچون فولاد کربنی و ایجاد جوشی با کیفیت، باید دستگاه های جوشکاری چسبی دارای الکترودهای مناسبی باشند. پایداری قوس الکتریکی، عمق نفوذ، نرخ نشست فلز و ظرفیت موقعیتی به شدت وابسته به ترکیب شیمیایی فلاکس پوشش داده شده بر روی الکترود میباشد. الکترودها را در سه دسته اصلی میتوان تقسیمبندی نمود:
- سلولزی
- روتیلی
- پایه
الکترود سلولزی
در پوشش الکترودهای سلولزی، مقدار زیادی سلولز وجود داشته و میزان نفوذ قوس در آنها عمیق بوده و سرعت بالای سوختن در آنها باعث افزایش سرعت جوشکاری میشود. نشست جوش در این الکترودها ممکن است درشت و همراه با سرباره سیال باشد؛ که امکان دارد سرباره گیری آن سخت شود. استفاده در هر موقعیتی از این الکترودها آسان و راحت بوده و به خاطر بکارگیری آنها در جوشکاری لوله های بخاری بسیار مورد توجه قرار گرفته اند. اگر به دستگاه جوش و برش علاقه مند هستید و میخواهید درباره آن اطلاعات کسب کنید، و یا قصد خرید دستگاه جوش و برش را دارید میتوانید از فروشگاه ایران بور اقدام کنید.
ویژگیهای الکترود سلولزی:
- نفوذی عمیق در هر موقعیت
- مناسب در جوشکاری عمود رو به پایین
- خواص مکانیکی نسبتاً مناسب
- تولید هیدروژن زیاد و درنهایت ایجاد ترک در منطقه متاثر از حرارت
الکترود رتیلی
الکترودهای روتیلی دارای مقدار زیادی تیتانیم اکسید (روتیل) هستند؛ حضور اکسید تیتانیم منجر به اشتعال راحت قوس، همواری قوس و پاشش کمتر میگردد. این الکترودها جزو الکترودهای عمومی با ویژگی و خواص جوشکاری مناسبی میباشند که برای هر موقعیتی میتوان با منابع تغذیه متناوب و مستقیم از آنها استفاده نمود. این الکترودها به صورت ویژه برای جوشکاری اتصالات گوشه در موقعیتهای افقی/ عمودی مناسب میباشند.

ویژگی های الکترود رتیلی:
- خواص مکانیکی متوسط فلز جوش مثل استحکام کششی
- ایجاد پروفیل مهره خوب از طریق سرباره ویسکوز (چسبناک)
- قابلیت جوشکاری موضعی با سرباره سیال (دارای فلورور)
- سرباره گیری آسان
الکترود پایه
در پوشش الکترودهای پایه میزان زیادی کلسیم کربنات (سنگ آهک) و کلسیم فلوراید (فلورسپار) وجود دارد؛ که منجر به سیالیت بیشتر سرباره این الکترودها نسبت به الکترودهای روتیلی میشود. انجماد سریع در این الکترودها باعث کمک به جوشکاری در موقعیتهای عمودی و بالاسری میشود. در جوشکاری قطعات متوسط و سنگین از این الکترودها استفاده میگردد؛ که در این قطعات نیاز به کیفیت بالاتر جوش، خواص مکانیکی مناسب و مقاوم به ترک (به خاطر مقاومت بالا) هست.
ویژگی های الکترود پایه:
- فلز جوش با هیدروژن کم
- نیازمند جریانها/ سرعت های جوشکاری بالا
- پروفیل ضعیف مهره جوش (پروفایل درشت و محدب سطح)
- سرباره گیری سخت
الکترود پودر فلزی
در الکترودهای پودر فلزی وجود پودر فلزی در پوششهای فلاکس باعث افزایش بیشینه میزان مجاز جریان جوشکاری میشود؛ از این رو، نرخ نشست فلز و بازدهی (درصد فلز نشست داده شده) برای اندازه مشخصی از الکترود نسبت به الکترودی با پوشش بدون پودر آهن افزایش پیدا میکند. سربارهگیری نیز به آسانی انجام میشود. الکترودهای حاوی پودر آهن به دلیل نرخهای بالای نشست، بیشتر برای موقعیتهای تخت و عمودی/ افقی بکار میروند. در الکترودهای روتیلی و پایه میتوان به بازدهی 140-130 درصدی بدون تضعیف مشخصههای قوس دست پیدا کرد؛ ولی کاهش نیروی قوس منجر به کاهش نفوذ مهره جوش می شود.
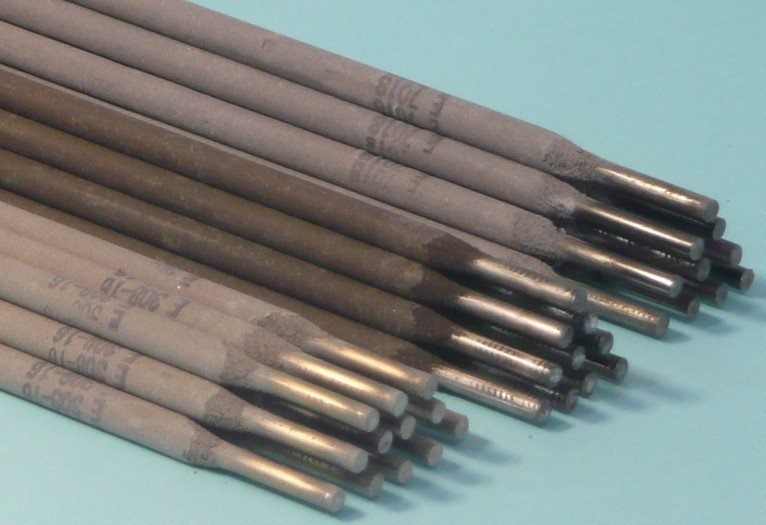
منبع تغذیه (دینام جوشکاری)
امکان بکارگیری الکترودها با منبع های تغذیه جریان متناوب و مستقیم وجود دارد؛ امکان استفاده از الکترودهای DC در منابع تغذیهAC نیست، اما الکترودهای AC در منابع تغدیه با جریان متناوب یا مستقیم میتوانند بکار برده شوند.
مطالب مرتبط و مفید:
جریان جوشکاری
میزان جریان جوشکاری از طریق اندازه الکترود تعیین میگردد؛ که سازندگان محدوده عملیاتی و جریان نرمال را پیشنهاد میدهند. در جدول محدوده های معمول عملکرد برای اندازه های مختلفی از الکترود ارائه شده است. هنگام انتخاب جریان مناسب جوشکاری، باید به این نکته توجه گردد که به طور کلی هر الکترود حدودا نیاز به40 آمپر در میلیمتر (قطر) دارد؛ از این رو، میزان جریان جوشکاری ترجیحی برای هر الکترودی با قطر 4 میلیمتر برابر با 160 آمپر است که محدوده 190-140 آمپر قابل قبول میباشد.
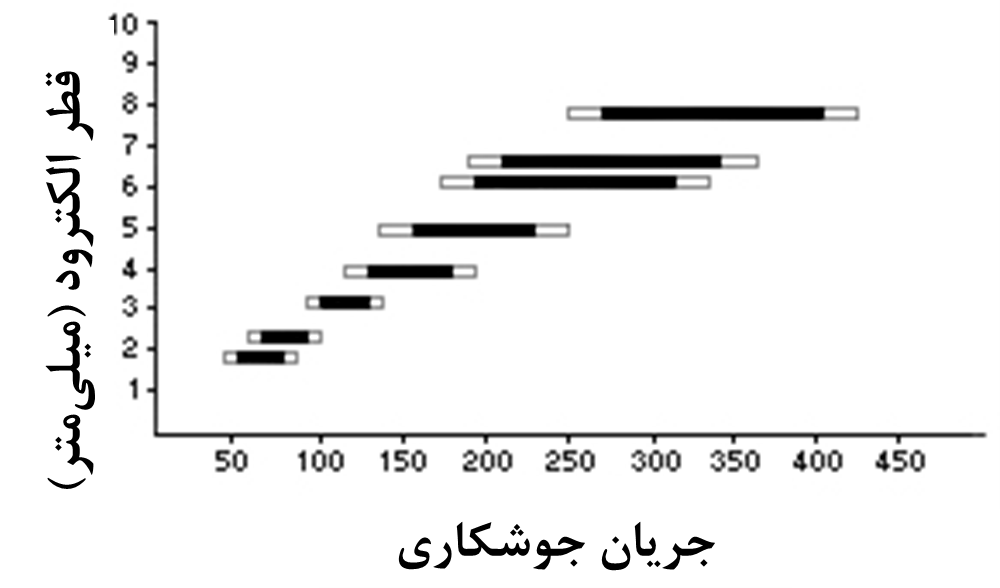
تکنولوژی های جدید
اکنون از طریق تکنولوژی ترانزیستور (معکوس کننده) امکان تولید منابع تغذیه خیلی کوچک و تا حدودی با وزن پایین فراهم شده است؛ این منابع تغذیه برای جوشکاری در محل بسیار پرکاربرد بوده و امکان جابجایی آنها از شغلی به شغلی دیگر وجود دارد. بخاطر کنترل الکترونیکی آنها، دسترسی به واحدهای اضافی در جوشکاری تنگستن گاز محافظ [MIG] و جوشکاری قوسی با گاز محافظ خنثی [TIG] باعث افزایش انعطاف پذیری میشود. در حال حاضر الکترودها در داخل محفظه های آب بندی شده موجود هستند؛ که وجود بسته بندی های تحت خلاء باعث عدم نیاز به پخت الکترودها پیش از استفاده میشود. اما در هنگام باز شدن محفظه و یا آسیب دیدن آن نیاز به خشک کردن دوباره الکترودها براساس دستورالعمل های سازنده هست.